Aluminum Spreading Solutions Unveiled: Crucial Insights and Tips
Discovering the realm of light weight aluminum casting solutions can unveil a globe of elaborate procedures and nuanced considerations that are essential for effective outcomes. As markets increasingly transform to aluminum for its light-weight yet durable properties, recognizing the essentials of casting comes to be critical. From the basic techniques to the complex details that can make or break a spreading project, there is a riches of understandings and tips waiting to be found. So, as we venture right into the realm of light weight aluminum spreading services, prepare to discover the vital elements that can shape the trajectory of your jobs and boost your understanding of this elaborate craft.
The Fundamentals of Aluminum Casting
What essential procedures are entailed in light weight aluminum spreading that create the foundation of this commonly utilized production method? Aluminum casting is a flexible and economical technique utilized in various industries to create facility and detailed steel elements. The process begins with the melting of aluminum ingots in a heater, typically at temperature levels varying from 1220 ° F to 1670 ° F, depending upon the certain aluminum alloy being used. As soon as molten, the light weight aluminum is put right into a pre-designed mold and mildew tooth cavity, where it takes the form and strengthens of the mold.
After solidification, the mold is removed, and the casting undergoes finishing processes such as heat surface, machining, and therapy finish to meet the called for specifications. Understanding these fundamental procedures is necessary for accomplishing top quality aluminum spreadings with specific dimensions and mechanical residential properties.
Different Casting Approaches Clarified
Exploring the numerous methods used in aluminum spreading offers important insights into the diverse approaches used to achieve intricate and specific metal parts. One common approach is sand spreading, where a mold and mildew is produced using compressed sand around a pattern of the desired component. This method is versatile and cost-effective, ideal for both basic and complicated shapes. An additional technique, die spreading, includes injecting liquified aluminum right into a steel mold under high pressure. Pass away casting enables high precision and repeatability, making it suitable for mass production of tiny to medium-sized components. For more complex designs, financial investment casting is often favored. This method uses wax patterns that are thawed away, leaving a cavity for the molten aluminum to load. Investment spreading yields specific details and smooth coatings, making it prominent in sectors like aerospace and auto. Each casting approach has its distinct benefits and is picked based on elements such as volume, expense, and intricacy considerations.
Factors to Think About When Selecting a Supplier
When selecting an aluminum casting service company, assessing their experience and proficiency is crucial for ensuring high quality and dependability in the production process. The carrier's experience in the area shows their knowledge with various spreading methods, prospective difficulties, and best practices. It is vital to ask about the kinds of projects they have actually dealt with in the past, ensuring they align with the intricacy and requirements of your very own job.
In addition, take into consideration the supplier's track record within the industry. Seek evaluations, reviews, and case researches that demonstrate their ability to provide top quality light weight aluminum spreadings consistently. A reliable carrier will often have qualifications or affiliations with sector organizations, showcasing their dedication to excellence and adherence to market standards.
Moreover, assess the supplier's capabilities in regards to customization, volume needs, and task timelines. Ensure that they can suit your specific requirements and have the flexibility to scale manufacturing as required. Efficient interaction and transparency concerning prices, lead times, and high quality control procedures are also important variables to consider when selecting a light weight aluminum casting company.
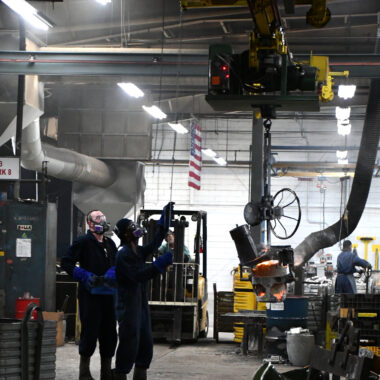
Common Challenges and Solutions
Navigating via the complexities of light weight aluminum casting processes often provides suppliers with a series of obstacles that call for ingenious remedies their explanation to guarantee performance and quality in production. One usual challenge dealt with in light weight aluminum casting is the formation of flaws such as porosity, shrinkage, or additions due to inappropriate mold and mildew design or insufficient steel top quality.
Another difficulty depends on attaining accurate dimensional accuracy, particularly for intricate geometries. Variants in cooling rates, mold growth, and product residential or commercial properties can lead to discrepancies from the designated measurements. Applying advanced technologies like computer-aided style (CAD) and computer numerical control (CNC) machining can improve accuracy and consistency in aluminum casting. Furthermore, preserving proper control over the melting and putting procedures is crucial to prevent issues like overheating or unequal distribution of the molten metal - casting aluminum. By buying automation and real-time monitoring systems, manufacturers can improve process control and minimize variations, inevitably boosting the total top quality of light weight aluminum cast products.
Tips for Optimizing Your Spreading Projects
By making sure that the gating system is well-designed and appropriately placed, you can enhance the circulation of molten light weight important source aluminum and minimize the possibilities of problems in the last casting. Furthermore, making use of computer simulations can assist in analyzing the flow and forecasting of steel during the casting procedure, permitting for adjustments to be made before real manufacturing begins.

Verdict
Finally, recognizing the basics of light weight aluminum spreading, various spreading techniques, variables to consider when selecting a provider, usual challenges and solutions, and suggestions for maximizing spreading projects are necessary for effective outcomes. By adhering to these insights and applying best organizations, people and techniques can ensure efficient and efficient light weight aluminum spreading solutions that satisfy their details needs and requirements.
Understanding these fundamental processes is essential for accomplishing high-grade light weight aluminum spreadings with specific measurements and mechanical properties.
When choosing an aluminum spreading solution carrier, evaluating their experience and competence is vital for making sure high quality and reliability in the production procedure. Efficient communication and transparency pertaining to expenses, lead times, and quality control processes are also crucial variables to think about when choosing a light weight aluminum spreading service provider.
Navigating via the intricacies of aluminum spreading processes frequently offers suppliers with a series of obstacles that need innovative remedies to guarantee efficiency and high quality in production. One typical challenge encountered in aluminum casting is the development of defects such as porosity, contraction, or inclusions due to inappropriate mold style or inadequate metal top quality.